To improve the quality of the dehumidifier, PREAIR continuously emphasizes details and caters to customer needs.
On December 26, 2024, the head of the Quality Inspection Department of PREAIR held a joint meeting to communicate with sales backbones about the plan for improving product quality for the coming year. In this year, our company provided bulk goods to more customers. We achieved impressive sales performance due to the trust of our existing customers and the strong interest of new customers in our products. As we all know, a 100% product qualification rate is almost impossible to achieve due to various uncertain factors. In the next year, PREAIR is committed to achieving industry-leading qualification rates for each batch of finished products.
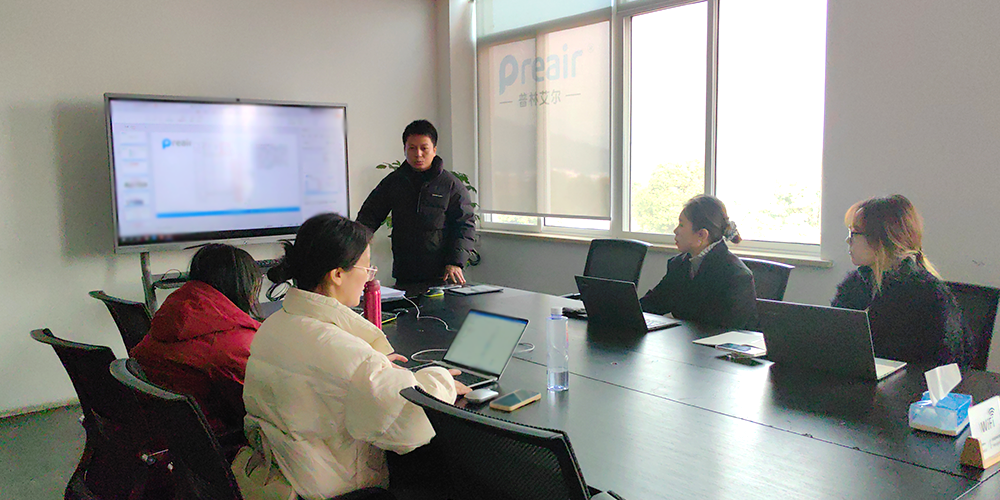
During the meeting, summarizing past experiences in manufacturing and customer complaint resolution, the head of the Quality Inspection Department found that it is vital to prioritize the quality of components procured from suppliers. In response, he proposed a Quality Inspection Plan for purchasing components by implementing a traceability responsibility system, and jointly developing a component standard through the efforts of the Quality Inspection Department and the Research and Development Department. Then, the Supply Chain Department selects suppliers based on the standard, and the overall process includes on-site inspections, sample trials, price negotiations, contract formulation, and factory inspections. Conducting factory inspections on suppliers has multiple benefits, such as ensuring that the quality of each batch of products meets the requirements, preventing from a high rate of defective products after receiving them, and avoiding defective components from being used in the dehumidifier manufacturing process. On the one hand, the implementation of this plan requires close cooperation between the Quality Inspection Department, Research and Development Department, and Supply Chain Department to avoid some predictable risks in the early stages of product production, greatly reducing the risk of exceeding the defective product rate of dehumidifier products. On the other hand, the Quality Inspection Department has proposed to increase budget investment in human and financial resources, including expanding the team of quality inspection leaders, and establishing service life laboratories for different series of machines, to create a full process quality inspection control team to collect first-hand information on machine use and establish a problem-solution database. Mr. Xue, the head of the Quality Inspection Department, said that 2025 is a year full of challenges and pressure. “We will spare no effort to promote the implementation of this inspection plan, improve the pass rate of finished products, reduce potential customer complaints, and become a strong support for the Sales Department.”
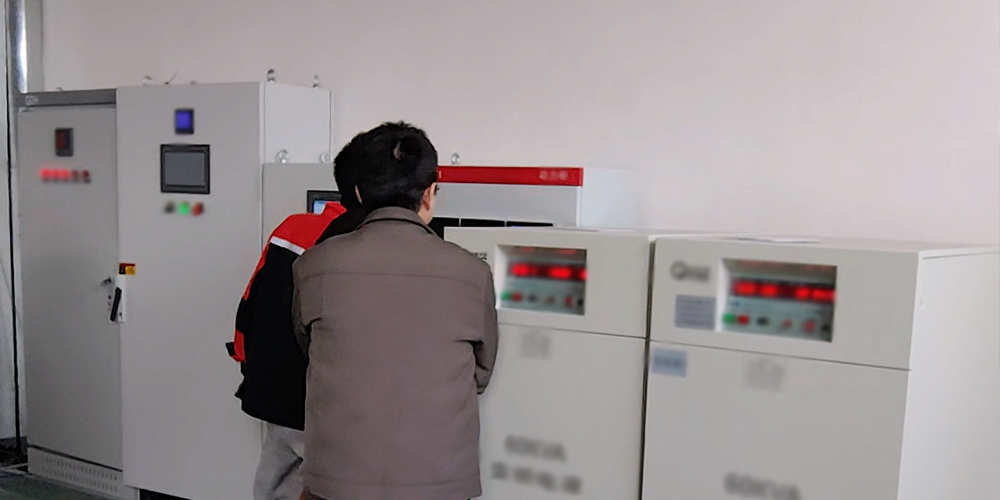
PREAIR has adhered to the development philosophy of "continuous innovation" all the time. We have created a virtuous cycle of constantly discovering problems, identifying causes, finding solutions, summarizing experiences, and avoiding problems from the source. Our development goal has been to "meet customer needs" since the beginning of our factory. The OEM and ODM orders received are primarily conducted according to customer needs. The strict and detailed requirements of our clients have greatly improved our work. Our process of integration with customers is a continuous process of development for both parties. If you ask why chose the PREAIR dehumidifier, I have to say that after more than 20 years of hard work, PREAIR has achieved its current scale through continuous innovation and the satisfaction of customers. The choices of numerous customers, huge production ability, and innovative ideas are PREAIR’s competitive advantages.
Post time: Dec-30-2024