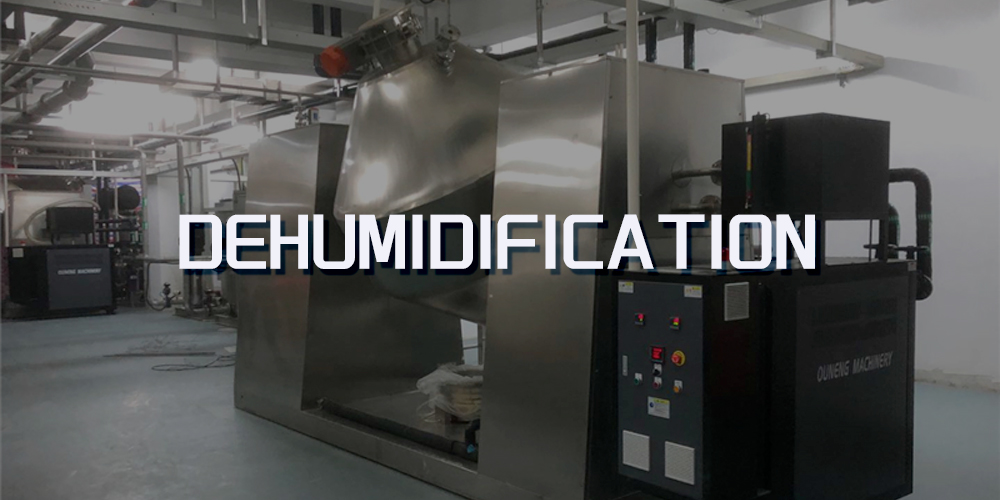
Lithium battery dry rooms are specialized environments used in the manufacturing of lithium-ion batteries, where extreme dehumidification is essential to ensure the safety, quality, and performance of the batteries. Moisture in the air can react with lithium-based materials, leading to safety hazards and reduced battery efficiency. Therefore, the dehumidification process in these dry rooms is crucial.
Here's how dehumidification is managed in lithium battery dry rooms:
1. Importance of Dehumidification in Lithium Battery Manufacturing
- Moisture Sensitivity of Lithium: Lithium is highly reactive with water. Even trace amounts of moisture can lead to:
-- Lithium hydroxide formation: This can reduce the electrochemical performance of the battery and lead to defects.
-- Safety hazards: Moisture can increase the risk of battery fires or explosions during the manufacturing process or in operation.
- Quality Control: Ensuring a dry environment improves the consistency and lifespan of lithium-ion batteries by minimizing the risk of contamination and ensuring uniform production standards.
2. Target Humidity Levels
- Ultra-Low Humidity Requirements: The typical relative humidity (RH) in a lithium battery dry room needs to be as low as 1% RH or lower, with some facilities aiming for less than 0.5% RH. These extreme levels ensure minimal water vapor content to avoid any reaction with lithium materials.
- The dew point (a measure of moisture in the air) is also critical. In dry rooms, the dew point is usually maintained between -40°C to -60°C (-40°F to -76°F) or even lower, depending on the manufacturing requirements.
3. Dehumidification Systems for Lithium Battery Dry Rooms
- Desiccant Dehumidifiers: These are the most common and effective systems used in lithium battery dry rooms due to their ability to achieve ultra-low humidity levels. Desiccant dehumidification involves passing air over or through a moisture-absorbing material (desiccant) such as silica gel or activated alumina, which captures the moisture from the air.
-- Regeneration Process: The desiccant material is regenerated by heating, which releases the absorbed moisture, allowing the desiccant to be reused continuously.
-- Multiple Stages: In some cases, a two-stage dehumidification system is used—one stage for initial moisture removal and a second stage for achieving ultra-low humidity levels.
- HVAC Integration: Dry room dehumidification is typically integrated with advanced HVAC systems designed for precise temperature and humidity control. These systems help ensure a stable environment with minimal fluctuations.
-- Air conditioning: While temperature control is not the primary function, it supports the dehumidification process by maintaining a cool environment, which helps lower the dew point.
- Recirculating Air Systems: These systems are used to continually cycle and treat the air within the dry room, preventing external air (which has higher moisture content) from entering the space.
4. Air Sealing and Control
- Airlock Systems: Entry to and exit from the dry room must be tightly controlled to avoid introducing humid air from outside. Airlocks or anterooms with sealed doors are used to minimize air exchange with the surrounding environment.
- Sealing Walls and Floors: The construction materials of the room should have low permeability to prevent any air leakage. Proper insulation and airtight sealing are essential to maintain the ultra-low humidity environment.
5. Air Handling and Filtration
- HEPA Filters: Air entering the dry room must be filtered through High-Efficiency Particulate Air (HEPA) filters to remove any airborne particles or contaminants that could affect the battery materials or production processes.
- Positive Air Pressure: To ensure that external, more humid air does not enter the room, a slight positive air pressure is often maintained. This ensures that air flows out when doors are opened, rather than allowing moisture-laden air to flow in.
6. Monitoring and Control Systems
- Humidity Sensors: Highly accurate humidity and temperature sensors must be installed throughout the dry room to monitor and control conditions in real time. These sensors should be calibrated regularly to ensure precise readings.
- Alarm Systems: An integrated alarm system is essential to notify operators if humidity levels rise above acceptable thresholds. Even small increases in moisture can pose a risk to the battery production process.
- Automated Control Systems: Modern dry rooms use automated systems that adjust the dehumidification process based on real-time data. This reduces the risk of human error and ensures that the environment remains stable.
7. Energy Efficiency in Dehumidification
- Dehumidifying a dry room to such low levels can be energy-intensive. To improve energy efficiency, heat recovery systems are often used. These systems capture heat from the dehumidification process (especially from desiccant regeneration) and reuse it in other parts of the facility.
- Variable speed drives (VSD) on fans and motors also help to optimize energy use by adjusting airflow based on the room's humidity conditions.
8. Common Challenges in Lithium Battery Dry Room Dehumidification
- Maintaining Consistent Conditions: Any variation in humidity, even for short periods, can compromise the quality of lithium-ion batteries. This makes constant monitoring and fine-tuning essential.
- Energy Consumption: Ultra-low humidity environments require a significant amount of energy, especially for large-scale production. Therefore, balancing energy use while maintaining performance is a critical concern.
- Seal Integrity: Ensuring that the dry room is perfectly sealed to avoid leakage of humid air can be challenging, especially in older buildings or retrofitted facilities.
9. Maintenance of Dehumidification Systems
- Regular maintenance and cleaning of desiccant materials and filters are crucial to keep the dehumidification system operating efficiently.
- The desiccant materials need to be regenerated or replaced periodically to ensure that they continue to absorb moisture effectively.
Conclusion
Effective dehumidification in lithium battery dry rooms is essential to prevent moisture contamination that can compromise battery quality and safety. The use of desiccant dehumidifiers, airtight construction, precise HVAC systems, and real-time monitoring ensures that the ultra-low humidity levels required for lithium-ion battery production are consistently maintained.
Post time: Oct-09-2024