Ⅱ. Key Aspects of Dehumidification in the Pharmaceutical Industry
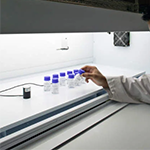
1. Product Stability:
Many pharmaceutical products are sensitive to changes in humidity. Excessive moisture can lead to degradation, reduced shelf life, and altered efficacy. Therefore, controlling humidity levels is critical to maintaining product stability.
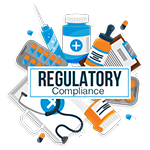
2. Regulatory Compliance:
Regulatory agencies such as the FDA (Food and Drug Administration) and other international counterparts have strict guidelines for pharmaceutical manufacturing. These guidelines often include requirements for environmental conditions, including humidity control.
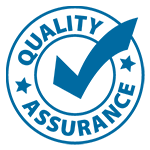
3. Quality Assurance:
Quality control is a primary concern in pharmaceutical manufacturing. Humidity control is one of the factors that can directly impact the quality of the final product. Deviations from specified humidity levels can result in batch rejections or recall.
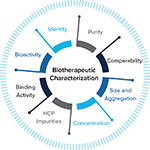
4. Manufacturing Processes:
Certain pharmaceutical manufacturing processes, like tablet compression and coating, can be adversely affected by high humidity. Inconsistent humidity levels can lead to problems such as sticking, capping, and lamination.
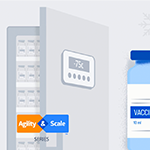
5. Storage Conditions:
Proper humidity control is vital during the storage of raw materials, intermediates, and finished products. Incorrect humidity levels can lead to moisture-induced degradation or spoilage.
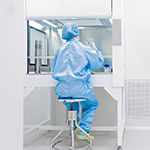
6. Cleanroom Environments:
Pharmaceutical production often occurs in controlled environments, such as cleanrooms. These environments require precise control of temperature and humidity to meet industry standards.
7. API (Active Pharmaceutical Ingredient) Manufacturing:
The manufacturing of APIs often involves the use of solvents and chemical reactions that can be sensitive to humidity levels. Maintaining controlled humidity is crucial to ensure the quality and consistency of the API.
8. Hygroscopic Materials:
Many pharmaceutical ingredients are hygroscopic, meaning they readily absorb moisture from the environment. This can affect their stability and performance, making dehumidification essential.
9. Packaging Considerations:
Packaging materials and processes may be sensitive to humidity. For example, paper-based packaging materials can swell or deteriorate in high-humidity conditions.
10. Energy Efficiency:
Dehumidification systems need to be designed for energy efficiency, as pharmaceutical manufacturing facilities often have stringent requirements for sustainable operations.
11. Monitoring and Validation:
Continuous monitoring of humidity levels is essential to ensure compliance with regulatory requirements. Additionally, validation processes are put in place to confirm that the dehumidification systems are functioning as intended.
12. Emergency Response Planning:
Contingency plans should be in place in case of equipment failure or unforeseen events that could lead to deviations in humidity levels.
It's important for pharmaceutical manufacturers to work closely with HVAC (Heating, Ventilation, and Air Conditioning) engineers and experts in environmental control systems to design and maintain dehumidification systems that meet the specific needs of their facilities and products. Additionally, regular testing, maintenance, and calibration of dehumidification equipment are critical to ensure reliable performance.
Ⅲ. How to Choose Dehumidifiers for the Pharmaceutical Industry?
Choosing the right industrial dehumidifiers for the pharmaceutical industry is a crucial step in ensuring product quality and compliance with regulatory standards.
1. Understand the Requirements:
- Review regulatory guidelines and industry standards to determine the specific humidity levels required for your facility. Different pharmaceutical products may have varying humidity tolerance levels.
- Consider factors like temperature, humidity range, and clean room classification requirements.
2. Capacity and Sizing:
- Calculate the required dehumidification capacity based on the size and layout of the facility, as well as the expected moisture load.
- Ensure that the industrial air dehumidifier can handle the maximum anticipated moisture levels during production.
3. Type of Dehumidifier:
- Desiccant or Refrigerant: Consider whether a desiccant-based or refrigerant-based dehumidifier is more suitable. Desiccant dehumidifiers are often preferred for low dew point applications and environments with very low humidity requirements, while refrigerant dehumidifiers are effective for moderate to high humidity settings.
- Preair provides types of dehumidifier for customers, retailers, wholesalers, and distributors. Industrial dehumidifiers for the pharmaceutical industry have a promised market in the world. The models of PRO series dehumidifiers have various dehumidification capacities that can meet almost all the requirements of enterprises.
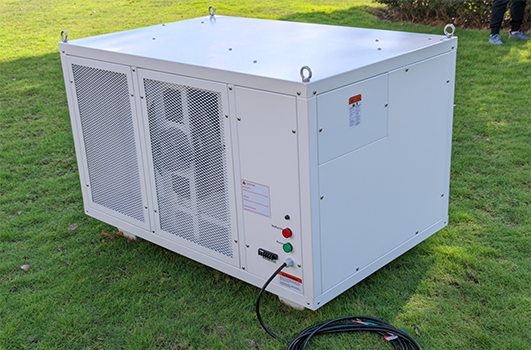
4. Compliance with GMP (Good Manufacturing Practices):
- Ensure that the chosen dehumidification equipment complies with GMP standards and other relevant regulatory requirements. This may include materials used in construction, ease of cleaning, and documentation capabilities.
5. Energy Efficiency:
- Opt for energy-efficient dehumidification systems to minimize operational costs and reduce environmental impact. Look for units with high Energy Efficiency Ratios (EER) or Coefficients of Performance (COP).
6. Installation and Integration:
- Consider how the wall mounted dehumidifiers will be integrated into your existing HVAC system. Ensure that they can be properly installed and ducted to provide uniform humidity control throughout the facility.
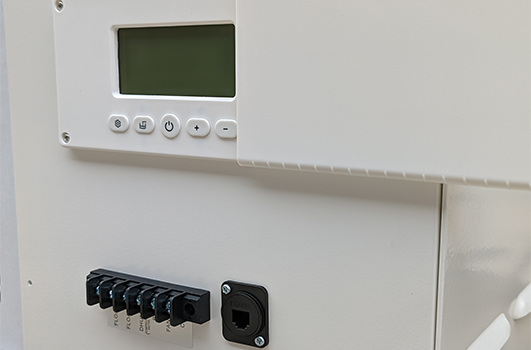
7. Control Systems:
- Look for a pharmaceutical dehumidifier with an advanced control system that allows for precise adjustment of humidity levels.
Preair's PRO500 dehumidifier can be controlled through APP, WiFi, Mod-bus, etc. Users can remotely control and monitor the condition of the pharmaceutical environment. The desired temperature and RH, and operation time and duration of the machine can be preset.
8. Maintenance and Serviceability:
- Choose equipment that is easy to maintain and service. This includes accessibility for routine maintenance tasks, availability of replacement parts, and access to technical support.
9. Validation and Calibration:
- Ensure that the dehumidification equipment can be validated and calibrated to meet regulatory requirements. This may involve periodic testing and documentation of performance.
10. Budget Considerations:
- While it's important to invest in high-quality dehumidifiers, consider your budget constraints and balance them with the performance and compliance requirements of the equipment.
By carefully considering these factors, you can select dehumidification equipment that meets the specific needs of your pharmaceutical facility, ensuring product quality and compliance with regulatory standards.
Ready to start a
Pharmaceutical Industry?
Post time: Sep-20-2023